Autodesk Inventor sketching quick tips
This weeks excellent guest post is from Inventor Guru, AU speaker and all round nice guy Mike Thomas.
If you feel a burning desire to write a blog post for Cadsetterout – please feel free to contact me.
Ahhh, sketching – the foundation of any 3D Parametric model,
and like a foundation if it falls down so does the entire building (model). Sketching is not always the most exciting part of creating your models but it is so important to robust models. Here are many tips, tricks, and time-savers that I have collected over the years…. tips that will make you more productive and get you building more robust models.
This is the second part of a series on sketching within Autodesk Inventor. You can find the first part to this series on Design & Motion:
5 Inventor Sketching Tips You Need to Know Right Now!’
The majority of the content is extracted from the 14+ years of my use with Inventor. I collected every nugget of information I could and put together a class, which I’ve presented the past two years at Autodesk University.
Creating Geometry
For many years the Inventor development team ignored AutoCAD, as why would a state of the art 3D modeling package need to do anything like an outdated dinosaur like AutoCAD…
Well the old veteran on the block still had a few tricks up its sleeve, a few gems that just leads to better productivity. These AutoCAD features are now a part of Inventor, they will save you time while sketching in Inventor.
Dynamic Input is a way of working with sketch geometry. It “provides a Heads-Up Display (HUD) interface near the cursor to help you keep your focus in the sketching area.”
Using the input boxes that appear as you are creating 2D geometry you to define the size of the object as you are creating it, which even creates the dimension. The key part of working with Dynamic Input is the TAB key toggles between the various options, whereas ENTER will accept the sizes.
Values entered become dimensions when accepted – dimensions are only created on the inputs you entered a value.
Bonus TIP: disable Persistent Dimensions if you don’t want dimensions created
To me anything, whether big or small, that saves time is a good thing as even the little time savers, over a day or week can add up.
- Just like AutoCAD, when pressing the Spacebar in Inventor repeats the last command.
- Just like AutoCAD, when drawing a line you can right-click and close the line.
- Similar to how with AutoCAD polylines you can switch between arcs and lines in the same command you can within Inventor drag in the line command to create an arc.
NEW TO 2015! Sketch Behavior Improvements – While creating sketch geometry, endpoints are created on the mousedown/click action instead of mouse up/release….. one of the greatest Inventor enhancements ever!
Creating sketch geometry within Inventor typically takes on a completely different approach than in AutoCAD. Within AutoCAD you normally trim, extend, copy, mirror, hack, slash, and do whatever necessary to create the required geometry in as little of time. In Inventor it’s more about sketching and allowing the parametrics to define the sizes.
However, Offset has many benefits in creating similar geometry, even though it works a bit backwards compared to AutoCAD. Offset creates geometry by offsetting existing feature edges. As a bonus tip you do not need to select the entire loop if you disable the “Loop Select” option on the right-click menu.
NEW TO 2015! Sketch Offset improvements – line, arc, or ellipse segments of the offset geometry are automatically removed as soon as they reach zero length… meaning no flipped or degenerated geometry is created
When sketching lines there are some press-and-hold options to generate constrained lines or temporarily switch into a tangent arc creation mode.
- If you press-and-hold off the end of any point Inventor will generate a tangent arc from that point.
- If you press-and-hold and drag away from a line or arc Inventor will create a perpendicular line.
- If you press-and-hold and drag tangent-like from an arc or circle you will create a tangent line. If you continue to press-and-hold as you create the line you can snap tangent at the other end as well.
Text can be added to any sketch and then embossed or extruded to add features to your model. This can be used to generate things like part numbers, dates, place of manufacture, brand names, and logos stamped, engraved, or etched into the component.
Sketched text can include model parameters meaning that as the parameters update so does the text. The location of the text can be parametrically positioned either by the insertion point or the text box can be enabled providing more fine-tuned positioning.
NEW TO 2015! Text Styles for sketch text are now available. Geometry Text functions similar but will conform the text to a selected object, for example wrapping the text to an arc.
Reusing Geometry
Why redo when you can reuse? AutoCAD geometry can be imported into your sketches and once it’s imported you can add dimensions and constraints as if the geometry originated in Inventor. You can even copy & paste to bypass the wizard.
Bonus TIP: Use Auto Dimensioning to apply the “easy” constraints like horizontal, vertical, perpendicular, and parallel.
By default when you project geometry from one part into another it is made adaptive and remains linked to the other component. While it is adaptive and associated with the other component you cannot make changes to the project geometry because it will update as the other component changes.
You can override this behaviour by holding CTRL while you are projecting geometry, the geometry will be projected fixed in place opposed to adaptive. Adaptivity has its pros and cons and can be a very powerful tool when you intend to use it. Unfortunately the default behaviour makes it too easy to accidentally or inadvertently adaptive.
You can disable the Cross part geometry projection options in the Application Options (Assembly Tab) to flip the default behaviour. With these options disable you’d have to hold CTRL when projecting geometry to make it adaptive.
I highly-recommend disabling the two Cross part geometry project options. Adaptivity is great when you need it but can quickly become a pain when you don’t. Plus, if you are creating adaptive cross-part relationships automatically the amount of adaptive relationships can quickly grow, unintentionally. Disabling these options make it so that you do not accidentally create adaptive, cross-part associative geometry.
Constraints & Dimensions
Constraints control the geometric relationships, such as parallel or tangent, between sketch entities. Sketch constraints are visible only while editing the sketch.
Always follow the KISS rule!
KEEP IT SIMPLE STUPID!
Stability before Size. Add constraints and then add dimensions. Consider accepting the default dimensions if you are expecting “big” changes to the size of your sketch geometry. To help avoid sketch flipping issues change the smaller dimension values first then move onto the larger ones. Remember that the first dimension sets the scale of the sketch!
Use geometric constraints as much as possible… apply constraints first, then dimension. Constraints typically represent the things that are assumed on a drawing when not dimensioned. Dimensions can clutter the sketch, constraints do not.
Be Lazy and keep it simple. There is a fine line between efficiency and laziness; Don’t try to be everything to everyone with one sketch. Instead of making one sketch to be used for every feature in the model, follow one of the golden rules of sketching – KISS – one sketch per feature.
Only create in the sketch what you can work with easily. The moment sketching becomes work to fully constrained your sketch is too complicated .
Fillets are best as features and should be avoided in the sketch, same with chamfers, mirroring and most patterns. These types of sketch elements over complicate the sketch and are better controlled as features. [Why are these tools there then? You may run into rare cases where you have to use them].
Fully Constrain Your Sketches! To quote Curtis Waguespack
“The importance of fully constraining your sketches in Inventor cannot be overstated.”
To make the behaviour of your Autodesk Inventor sketches more predictable, constrain your sketch to the ‘Origin’ (0,0,0).
BONUS TIP: You can have Inventor auto-project the origin point by enabling ‘Auto project part origin on sketch create’. [Tools>Application options>Sketch tab]. Be careful with fix constraints, you should never need more than one.
The Horizontal & Vertical constraints can be used to align points either horizontally or vertically. The center point shown below is constrained so that it lines up horizontally with the midpoint of the vertical line and vertically with the midpoint of the horizontal line. The circle will remain constrained to these points even as the rectangle changes in size. This provides a great alternative to construction geometry or relating dimensions.
Make Automatic (Inferred) Constraints work for you.
Constraints are automatically applied as you sketch but you can make this work in your favour. This auto-constraining is referred to as constraint inference. What Inventor infers is dependent on the existing geometry, the type of object you are creating, the Constraint Options, and if Constraint Persistence is enabled.
You can adjust the geometry the auto-constraint is being inferred from by hovering (rubbing) over another object. For example, if your new line is snapping parallel (without exiting the line) you can hover over a line 90-degrees to it and your new line will now snap perpendicular.
If your new geometry is inferring constraints in a fashion you do not want you can hold CTRL as you sketch and no constraints (except for coincident) will be automatically created. You can then add the constraints of your liking. Additionally you can disable Constraint Persistence on the Constrain Options dialog
Constraint Options (available on the Constrain Panel) control which constraints will be inferred during sketching
Auto Dimension can be a quick way to determine where you are missing constraints. When you are missing constraints and just can’t seem to figure out where the 1 or 2 constraints are missing the Auto-dimension feature can quickly find the missing constraint location by adding dimensions to these objects.
Use Degree of Freedom to find under constrained geometry.
Use Degree of Freedom to help find unconstrained, partially constrained or fully constrained geometry.
Easiest method to access is via the right-click menu “Show All Degrees of Freedom”. The DOF symbols will update as you constrain your geometry
Dimension Smartly
Center lines can be used to create Revolved Sketch Dimensions, which is a great way to dimension revolved parts like Shafts.
You can create tangent dimensions if you know where to pick (keep moving until you see the icon change).
Save a step and build more intelligence by naming your parameters on the fly.
Other Tips, Tricks, and Suggestions
Use Sketches and Sketch Points to build hole patterns. Any point in the sketch can be used as a hole center (not just hole centers) and you can quickly change points to hole centers by selecting the points and adjusting their format.
There are many opportunities where using rectangles, polygons, and / or offset can create the basis of hole patterns more easily, smarter, or in cases where the hole pattern is non-rectangular or non-circular.
Any face in the model or any flat pattern can be exported to DXF. Any face in the model or any flat pattern can be exported to DWG or DXF avoiding the need for a drawing.
Whew! There are many of my tips, tricks, and nuggets of information to make you a better sketcher, a smarter sketcher, a sketcher of robust – intelligent models.
We’d love to hear your tips and tricks, post them to the comments and we can all share. Also, don’t forget to check out Paul’s 101 Inventor Tips… a lot of great stuff in it!
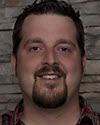
Mike graduated as the Most Distinguished Graduate from the CAD/CAM Engineering Technology program at SIAST.
He is specialist in the manufacturing industry with strong knowledge on the Autodesk manufacturing products supplemented with a solid understanding of document management, hardware, networking, and other technologies.
Mike is now the Technical Services Manager for Prairie Machine & Parts Mfg. and is a regular contributor www.designandmotion.net.
In his spare time Mike will be found with his wife and four daughters. You can contact Mike via Twitter @Aurbis
Thanks , very nice article )
Thanks Alon,
I’ll pass that on to Mike :D
Really nice,
A lot of info and well written. I was unaware of using CTRL to brake/link projected edges but I’ve disabled any background running hogs like adaptive and all from day one.
Thank you Mike, and Paul for another great post.
Adrian.